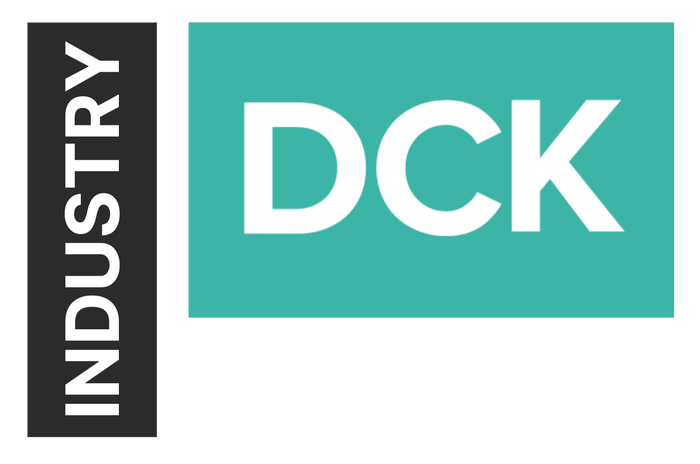
Insight and analysis on the data center space from industry thought leaders.
US Manufacturing Needs an ‘AI Backbone’ to CompeteUS Manufacturing Needs an ‘AI Backbone’ to Compete
To stay competitive, the US must rethink how it creates its AI backbone, leveraging software-driven automation, end-to-end data visibility, and nurturing a new talent ecosystem.
March 13, 2024
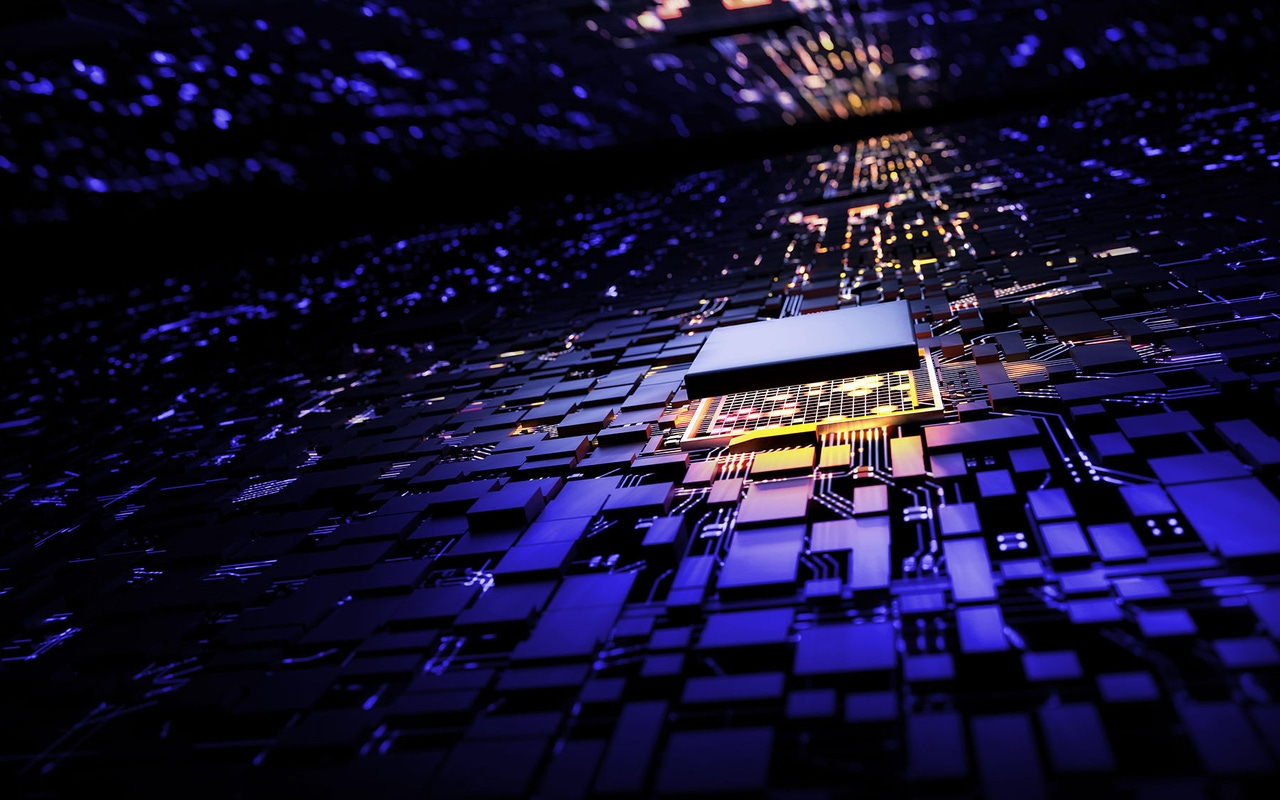
The recent boom in generative AI holds the promise of catalyzing a new era of innovation that can augment nearly every industry. Analysts are projecting a potential boost of nearly $7 trillion to the global GDP and a 1.5% increase in productivity over the next decade.
But US competitive potential could be left unrealized if we don’t rethink the manufacturing capacity to build its infrastructure.
Currently, cloud compute providers and data centers are struggling to keep up with demand to assemble and deliver compute, data storage, and network equipment – what we call the “AI backbone.”
The vast majority of assembly processes for this necessary hardware are rooted in the past: manual, reliant on fragmented global supply chains, and can't keep up with the agility, scalability, and precision needed for modern AI hardware.
Consequently, companies are facing difficulties in scaling infrastructure to support the demanding AI workloads, leading to production bottlenecks and suboptimal performance. This inevitably leads to delays, which hinders businesses from meeting customer demand.
To stay competitive, the US must rethink how we make our AI backbone. We need to drastically speed up ideation to assembly to keep up with the rapid pace of AI progress. Here's how we'll do it:
Software-Driven Automation
Traditionally, automated assembly processes have been limited to single-purpose, repetitive tasks without the real-time ability to detect deviations or inspect parts for quality. Silos and lack of standards across the manufacturing value chain have also led to quality issues, lack of transparency, and delays. It can take months to set up a new server. It doesn’t have to.
The industry needs a new standard, full-stack solution. As hardware has grown increasingly complex, US manufacturing needs software-driven solutions to enable more flexibility in the way it assembles products, like servers.
The automation technology itself within the solution should use machine learning and computer vision, fed by sensor data in real time, to drive automation in inspection and navigation. Innovations in sensors provide high-precision execution. This software-driven approach adds the flexibility necessary to assemble different servers of different designs and brands on the same line, and adaptability when products need upgrades or iterations over time.
End-to-End Data Visibility and Insights
This full-stack solution introduces a streamlined approach to manufacturing, emphasizing the importance of establishing repeatable, reference architectures across the entire manufacturing ecosystem, from chip designers to contract manufacturers, ODMs, and ultimately, the end customer.
This standardization is crucial for achieving comprehensive data visibility and insights throughout the production process. There's a growing consensus within the manufacturing industry about the necessity of integrating cloud-enabled data and performance analysis tools to enable faster and more efficient assembly operations.
Through cloud-enabled services, centralized management and analysis of manufacturing data are facilitated, characterized by standardized assembly processes, established quality standards, end-to-end visibility for chip designers, standardized data collection and processing methods, and enhanced data availability across the product lifecycle.
Fueling a New Talent Ecosystem
When it comes to attracting new talent, many post-graduate individuals are tech-savvy and seek opportunities at dynamic startups prioritizing emerging fields like generative AI and robotics. Modern manufacturing lines now automate tedious assembly tasks that were previously manual, like pick-and-place operations for CPUs or server DIMM card insertion. This advancement enables existing manufacturing workers to focus on higher-level tasks, such as line monitoring.
Offering roles in automation and robotics not only positions skilled US industrial positions as attractive long-term career paths but also boosts the nation's competitiveness in the global AI development landscape. This focus on training and developing new skills will not only attract fresh talent but also reinforce the manufacturing ecosystem, fostering further growth and resilience.
Closing Thoughts
Using old methods to build innovative tools will lead to decades-long stagnation. However, if we rethink our approach to building the AI backbone, we can fully realize the transformative potential of this significant paradigm shift, potentially the biggest since the Internet.
Lior Susan is CEO and Co-Founder of Bright Machines, and Founder and Partner at Eclipse Ventures.
Read more about:
North AmericaAbout the Author
You May Also Like